Rubriek: Glazen verhalen van GlassJohs
De Vikingen komen! rechts: de ontwerptekening en de uitwerking
vervolg: • versterking • foliewikkelen • solderen • reinigen en afwerken • transportklaar maken
• versterking
Het raam meet bijna anderhalve meter tussen elk der tegenoverliggende zijden. Bij zo'n formaat is het glas kwetsbaar. Als het geplaatst is, zal het voldoende stijf moeten zijn. Voordien moet het goed hanteerbaar zijn bij keren, reinigen, transporteren en plaatsen in het kozijn. Dat vraagt extra maatregelen. We kiezen voor twee specifieke bewerkingen: koperstrip en een stalen frame.
a. koperstrip
Er worden langs sommige lijnen flexibele koperstrips van 3 mm breed mee gesoldeerd. Deze strips worden verticaal tussen de glasdelen geplaatst, zie foto's hieronder. Ze moeten de druk absorberen die onwillekeurig op het glas uitgeoefend wordt bij de bewerkingen. Voor het advies dank aan Samantha Schofield Calder van Living Sun Glass (Canada)
foto's rechts: de koperstrip, en uiterst rechts de tekening met donker gemarkeerd de lijnen waarlangs de strip wordt aangebracht. Er is een opdeling in compartimenten gemaakt.
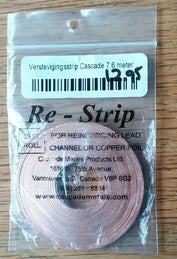
het aanbrengen van de koperstrip volgens het schema, met compartimentering van het tafereel en doorlopende lijnen van rand tot rand
de strip is buigbaar in de vorm van de lijn waarlangs hij komt te liggen. 'Moeilijke' vormen of scherpe hoeken veroorzaken zo geen spanning of druk tussen de glasdelen
de versterking wordt verticaal aangebracht en meegesoldeerd waardoor eventuele druk op het glas wordt opgevangen en afgeleid
b. een stalen frame
In overleg met het constructiebedrijf wordt gekozen voor een robuust stalen U-profiel. De 'bodem' van de U is 15mm breed, binnenin 9 á 10 mm. Dit frame komt om het 8mm U-profiel randlood dat al om het raam zit en waar ook al een staalstrip van 2 mm dik in opgenomen is. Het wordt in twee delen met elk 4 zijden gemaakt en in het atelier om het raam gemonteerd. De delen worden verbonden door 4 plaatjes, zie de rode hoekjes op de tekening. Die worden erop gelast en met 8 schroefjes verbonden aan het andere deel (foto's rechts).
Het staal is gepoedercoat in de kleur verkeerswit, waarmee het een slagvaste beschermlaag heeft. In het frame wordt aan beide zijden een PVC foamstrip aangebracht om de ruimte tussen glas en frame op te vullen (om evt. rammelen te voorkomen) en om enige vering aan te brengen.
De omlijsting gaat het raam de noodzakelijke stijfheid geven. Het zal vervoer en plaatsing in het kozijn vergemakkelijken. Voor het transport wordt speciaal een krat gebouwd, daarover later meer.
tekening: D. van der Molen, DWM Constructiebedrijf te Nieuweschoot
• foliewikkelen


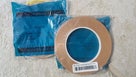
Elk der 300 delen moet voorzien worden van een randje koperfolie, de ondergrond waarop straks de tinlijnen gesoldeerd worden. Het materiaal is er op verschillende breedtes waardoor de breedte van de tinlijnen beïnvloedbaar is. Grote glasdelen krijgen in het algemeen breder folie dan kleine. Het glas is volgens specificatie 3 mm dik, maar de realiteit is een variërende dikte tussen 2,5 en 3,5 mm, aangezien het hier een mondgeblazen soort betreft. Dat heeft bij gelijke foliebreedte direct gevolg voor de dikte van de tinlijn. Lastig, want je wil geen variatie in lijnbreedte als gevolg van wisselende glasdikte. Die variatie wil je helemaal zelf bepalen: verschil in lijnbreedte maakt het tafereel natuurlijker en het suggereert dieptewerking.
Bij dun glas wordt smaller tape gebruikt dan bij het dikkere; voor (zeer) kleine glasdelen wordt dun folie gebruikt, voor grote iets dikker. Hoe dunner de folie, hoe makkelijker het de vorm van het glasdeeltje volgt. Maar het is ook kwetsbaar bij het aanbrengen. Hier baart oefening kunst.
Helder en licht gekleurd (doorzichtig) glas wordt voorzien van folie met een zwarte plakzijde. Van de gewone tape zou de koperkleur door het glas heen zichtbaar kunnen zijn en zo een onbedoelde werking krijgen. De zwarte binnenkant daarentegen wordt één geheel met de tinlijnen.
De veeleisende uitvoerder heeft behoefte aan meer foliesoorten: minstens 4 breedtes op diverse diktes; de smallere (voor kleine glasdelen) ook in heel dun folie; en dan alles zowel met koperkleurige als zwarte achterkant.
foto's onder: door het slijpwerk sluiten de glasdelen nu goed aan; alles is in de folie gezet, de toekomstige tinlijnen worden zichtbaar. Klik de foto's om het beter te zien.
• solderen
Hoeveel meter moet er gesoldeerd worden? Hoeveel tinsoldeer gaat er doorheen? Hoeveel flux? Hoe lang gaat het duren? Wat is de invloed van de breedte van de folie?
Allemaal vragen waar ik me nooit zo om bekommer bij het maken van een Tiffany-werkstuk. Het is altijd een beetje van dit, een stukje van dat. Mijn inschatting was dat ik een kilootje tinsoldeer nodig zou hebben. Voor de eerste zijde ben ik daar al ver overheen.
Het ontwerp vraagt qua lijndiktes een zorgvuldige benadering. De breedte varieert nogal binnen het ontwerp. Tussen de golven mag de lijn wat robuuster zijn, een contrast met de tinlijnen in het zeil. De schilden zijn samengesteld uit kleine glasdelen, daar horen nog dunnere tinlijnen bij. Iets bredere lijnen vooraan tegen dunnere achterin, suggereren diepte. Bij het folie-wikkelen wordt daar al rekening mee gehouden; hoe breder de folie, hoe dikker straks de tinlijn. Met het scalpelmesje worden vóór het solderen de laatste correcties aangebracht. Het gaat er altijd om dat de lijndikte niet 'toevallig' ontstaat, maar dat er gebeurt wat je voorziet. Dat gaat best ver, want het is lastig daar in de ontwerptekening al rekening mee te houden. Variabele foliebreedtes en scalpel zijn hier dus de bijkomende hulpmiddelen.
Door alle noodzakelijke bewerkingen rijgen de uren van staan en langer staan zich aaneen. Onwillekeurig sta je niet altijd in een ergonomisch verantwoorde houding. Het is heerlijk even lekker door te werken als de flow er is. Geldt niet alleen voor het solderen. Snijden, slijpen, foliewikkelen, als het voorspoedig gaat, is stoppen moeilijk. Je wil doorgaan en doorgaan. Ik heb het beperkt tot 3 á 4 dagdelen per week, 4 maanden lang. Voor de afwisseling werk ik ook dagdelen elders, in een heel andere discipline. En voor de conditie: 's morgens vroeg, 2 x per week, 5 kwartier 'nordic walken'. In april een weekje vakantie genomen, in juni een paar dagen fietsvakantie. Nothing but quality-time!
Tussen twee haken: 4 dagdelen glasbewerken à 4 u. per week, 16 weken lang = 16 x 16 = 256 uur. Ik ben er nog niet, het gaat wel naar de 300 uur. Wat mag een ambachtsman verdienen? 40 euro per uur? Da's 12.000 euro. Mmmmm, ik klaag niet, maar dat stond lang niet op de offerte. Dit is het niet zo droevig lot van de handwerksman. Onbetaalbaar immers om zo'n mooie klus te mogen uitvoeren.
Uitdagend ook: bij dit grote formaat moeten technische problemen opgelost worden die bij klein tiffanywerk geen rol spelen, zoals de noodzaak tot versterking, en het keren om de tweede zijde te kunnen solderen. Daarover later meer!
Soldeer bestaat uit 60 % tin en 40 % lood. Het smeltpunt ligt lager dan dat van lood, waardoor het goed te verwerken is op lood. Bij Tiffany werkstukken is er niet altijd lood in de buurt, er zijn andere zaken waar op gelet moet worden. De soldeerbout heeft een 'stand-by' en een 'werk'-temperatuur. De eerste is hoger waardoor het tin aanvankelijk snel smelt, bij de werktemperatuur hebben we de ideale omstandigheden. De temperatuur in de punt wisselt voortdurend doordat de warmte snel afgevoerd wordt tijdens het soldeerproces. Een goede soldeerbout heeft de capaciteit om de warmte snel aan te vullen, en zo de bedrijfstemperatuur op peil te houden. In de praktijk is het goed om regelmatig te onderbreken om de soldeerpunt te reinigen en om de bout weer op bedrijfstemperatuur te laten komen. De tin moet goed en regelmatig vloeien om mooie bolle lijnen te verkrijgen. De lijnen worden regelmatig en glad als de soldeerbout in het juiste tempo voortbewogen wordt bij regelmatig vloeiend tin. Uitvoerder zal tin en bout goed moeten 'lezen' om het mooiste resultaat te verkrijgen.
Een drieëenheid dus van tin en bout en uitvoerder. Maar dan is er nog het glas. Drie mm dik materiaal dat makkelijk kan breken en dat niet tegen hitte kan. Wat een uitdaging om dat te bewerken bij een temperatuur van 350° C. Een wonder dat al die tinlijnen verschijnen zonder een barst te veroorzaken. Het is wel zaak de soldeerbout te blijven bewegen, niet talmen op één plek... en zeker waar 'gesmokkeld' is met tinlijnen dwars over het glas, omdat de ontwerper in zijn tekening scheidslijnen aanbracht in dezelfde glassoort. Juist daar lijkt de kans op barsten het grootst: de bout beweegt immers niet langs de rand, maar dwars over het glas. Ook hier zoekt de bewerker de grenzen op van wat het materiaal kan hebben. Ervaring doet hem het glas 'lezen' en zo weet hij hoe ver hij gaan kan... op hoop van zegen, want het onverwachte komt nu eenmaal onverwacht.
Verbazing resteert over het onbewogen blijven van het glas ondanks de blootstelling aan zulke hoge temperaturen. Een zucht van verlichting ontsnapt aan GlassJohs als al die kwetsbare stroken van het rood-witte zeil na het solderen ongeschonden zijn. Maar ja... dit was pas de eerste zijde.
• het 'keren'
Als het frame eromheen zit, gaan we het raam keren. Normaal gesproken is dit het 'Magisch Moment' omdat een raam in deze fase voor 't eerst rechtop staat, en het licht erdoor komt. Je ziet eindelijk waar je voor gewerkt hebt! Weinig magie deze keer, het raam zit tussen planken, en uitstekende delen zijn bedekt met folie.
Bij dit formaat is het keren een delicate klus. De glasdelen bewegen nog enigszins ten opzichte van elkaar, omdat maar één zijde gesoldeerd is. Lange lijnen in het ontwerp kunnen gaan 'scharnieren'. In horizontale stand dreigt door het eigen gewicht voortdurend breuk. Het raam moet gesteund worden, boven en onder worden planken erlangs geklemd. Het totaalgewicht zal gauw 40 kilo zijn. Met drie mensen lukt de keer-klus. Nu ligt de echte voorkant boven. Alle folielijnen worden nagelopen en aangepast waar nodig. Het bruine glas van de kiel heeft een zeer gestructureerde bovenkant, lastig om de folie in de kiertjes te laten hechten. Bij het solderen blijkt ook wel hoe moeilijk het is om de lijnen strak te krijgen op het bobbelige bruine glas. Alweer een uitdaging. Deze tweede kant is nu ook klaar. Voor beide zijden is in totaal ruim 2 kilo soldeertin gebruikt.
Tussen frame en glas wordt een PVC schuimrand aangebracht (foto onder). Die zorgt voor enige 'vering' binnenin, en het voorkomt gerammel. Daarna opnieuw keren om de achterkant nogmaals onder handen te nemen; ook hier wordt een schuimrand ingebracht.
isolatie tussen frame en glas
• reinigen, finale check, signering
Het raam is klaar als het klaar is. Of niet? Na de laatste schoonmaakbeurt nog maar een check: geen 'doorgelekte' soldeer? Fluxresten? Alle aantekeningen, hulplijnen en nummeringen verwijderd? Dan volgt de ultieme afsluitende handeling, signering: Facit Studio GlassJohs 2018
Met behulp van de planken wordt het definitief rechtop gezet. Vanaf nu blijft het in deze positie: verticaal tijdens transport en plaatsing in het kozijn.
Het raam kan de kist in, de Vikingen komen, de Vikingen gaan.
• transport en plaatsing
voor het transport is een speciale krat gemaakt
Het raam gaat op reis naar de buurtschap Lyngen, gemeente Lyngseidet, Noorwegen. De route via Zweden is 2800 km. Op de foto middenonder een voorproefje van het resultaat. In de Vikingcabin van opdrachtgever Haakon Karlsen, waar zijn jonge onderzoekers van MIT FabLab Norway bijeenkomen, is tijdelijk een kleurenprint in het raam geplakt. Rechtsonder het moment van plaatsing. Helemaal onderaan het raam in vol ornaat in 'The Great Hall'. Het was mij een genoegen de glazen versie te mogen maken. Dank Rudie van der Meer voor de bemiddeling. Dank Haakon Karlsen Jr. voor het vertrouwen bij het verlenen van deze opdracht.
de route gaat tot ver boven de poolcirkel voorproefje van papier, buitenkant de plaatsing aan de binnenzijde
Het raam gemonteerd in de Vikingcabin in Lyngen, Norway
vakantie boeken in een Viking-blokhut:
Viking Cabins | Lyngen Alps | Norway
'De Vikingen komen'
Tiffanywerk in 297 delen
formaat 1469 x 1469 mm
i.o.v. H. Karlsen jr., Lyngseidet, Noorwegen
Viking Cabins | Lyngen Alps | Norway
© Atelier GlassJohs 2018
Colofon
'de Vikingen komen!'
formaat 1470 x 1470 mm
300 glasdelen
Techniek: Tiffany
Standplaats: Lyngen, Noorwegen
2018 © Atelier GlassJohs